Why low-code is the best code
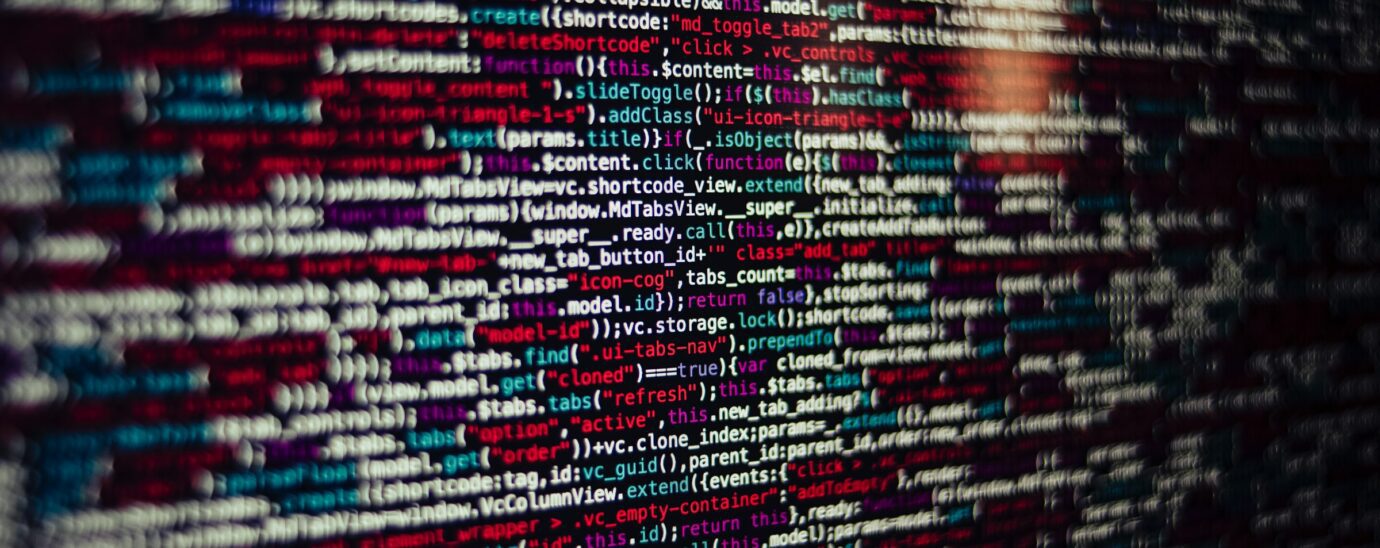
According to Gartner, over 50 percent of medium-to-large enterprises will adopt low or no-code platforms as part of their overall IT strategy by 2023. Low-code platforms are increasingly popular because they help organizations to deliver capabilities faster, reduce reliance and pressure on the workforce and are simpler to understand. Implementing an IoT strategy is not easy, but low-code platforms help to set up the foundation for a robust data management process. Here, Johan Jonzon, CMO and co-founder of low-code edge analytics platform Crosser, breaks down how industrial manufacturers can harness the potential of low-code.
“Five Ants are More than Four Elephants” was a Swedish children’s TV series that was produced in the 1970s. It was an educational program that was once hailed as the best children’s program ever produced in Sweden. While this might seem to be unrelated to the Industrial Internet of Things (IIoT), Crosser saw an opportunity to connect the two, with the belief that elephants must be eaten in small pieces. In IIoT applications, this translates to starting with small projects that are easy to implement and complete, then gradually building up to more advanced use cases. Simply put, eat the elephant in small, ant-sized pieces — don’t swallow it at once.
Operations in manufacturing are complex and plant managers have access to a lot of data. But their downfall is not knowing how to effectively manage the data their facility produces. This makes implementing IIoT use cases challenging. With the right tools it’s easy to start smaller and simplify, as it requires little effort to implement. Then over time, more advanced features can be added.
Why low-code is the best code
One of the simplest, yet highly effective technologies industrial manufacturers can implement is a low-code analytics platform. Instead of relying on extensive coding languages, low-code platforms use visual interfaces with simple logic and drag-and-drop features, requiring users to master a single system, rather than several. The simplicity of low-code means it is easier to use, so anyone working in a facility can make use of the platform. According to a recent report by Cloud computing company Appian, 84 percent of companies have turned to low-code tools to reduce the strain on their IT departments. Sharing the workload allows IT problems to be distributed across the organization, easing pressure on individual employees and teams — improving worker efficiency and saving costs.
Low-code platforms have even been adopted by globally recognized Time magazine to address the repetitive, manual processes in its vendor management process. Through a variety of low-code applications, Time reduced its invoice submission-to-payment cycle from months to days and streamlined vendor communications. But how can these types of platforms be used in industrial environments?
Applying this is manufacturing
Naturally, it can be hard to keep up with industry trends. But when this happens, gaps begin to show in the workforce. In today’s Industry 4.0 era where digitalization is key to gathering valuable data insights and optimizing processes, the workload for IT departments has increased substantially. In fact, the 2021 Connectivity Benchmark Report by Mulesoft found the number of projects IT teams are asked to deliver has increased by at least 30 percent year-on-year since 2017.
As a result, IT departments are struggling to meet demand because of the lack of developers throughout the industry. This has created an IT delivery gap, the space between the demand and the delivery capacity. Mulesoft’s report also indicated that less than four in ten IT teams fulfilled all
of their project commitments to business stakeholders. Low-code platforms reduce reliance on developers and IT specialists, which has numerous advantages. With more than half of IT projects completed late, low-code speeds up development time with pre-built integrations, which are straightforward to use.
Because of the simplicity, external coders and developers are not required to provide input or feedback on IT projects, which can be handled by other members of the workforce.
Furthermore, all manufacturers industry-wide will agree that the need to minimize costs where possible is a top priority. Using edge analytics can reduce equipment failures, resulting in reduced maintenance and downtime costs. For instance, the data a machine produces creates the opportunity for preventive maintenance business models in manufacturing. Assets on the shop floor continuously create alerts to notify enterprise systems about inconsistencies or faults in the machines, allowing time for issues to be resolved before unplanned downtime. In fact, the report by Appian also found that nearly 50 percent of businesses surveyed reported reduced cost using low-code platforms.
Fighting complexity with simplicity
While implementing low-code IIoT technologies is the first step to
a more effective and productive facility, it’s not possible to succeed if the data and how to act on it is not understood. So how do manufacturers turn this data into valuable insights that can be used to improve operations? To gain real insight, manufacturers must analyze the data that’s collected. This is done by first calculating key performance indicators (KPIs) — measurable metrics that enable organizations to determine what’s most important, identify inefficiencies and improve future process runs.
This will vary between manufacturers, but the most significant KPI all manufacturers should measure is overall equipment efficiency (OEE), which combines three KPIs in one: availability (A), performance (P) and quality (Q).
Availability is a measure of how long a machine operates out of the total available time. Take for example a machine that may have been required to run continuously for eight hours a day, but only operated for one hour. This could be because of machine maintenance and consequential downtime. Next, a machine’s performance is measured by the number of units it produces within the desired time frame, against the optimal number of units it should be able to produce. The final part of the equation, quality, measures a machine’s yield. This is calculated by the ratio of products produced that can be used without requiring rework or being scrapped.
Once the KPIs are identified, the next step is to determine a system that will analyze and process these results. A low-code edge analytics platform, like the one from Crosser, enables data produced by sensor-rich assets like machines, equipment and devices to be pre-processed in real-time — closer to where it is created — the edge.
The reduced distance between the server and end-user enables quicker analysis and decision-making. By processing at the edge, in real-time, KPIs can be generated and manufacturers can quickly overcome areas of inefficiency within equipment to ensure productivity is consistent.
Part of the platform involves a module library, which contains pre-built modules and connectors to help build intelligent data workflows. Fighting complexity with simplicity, the workflows are built using a simple drag and drop functionality. The module library is designed to implement common functionalities for manufacturing use cases, from connecting, to technical protocols to integrate data into any industrial system. In fact, there are modules specifically targeted to KPI calculations.
When combined with data aggregation modules from machines to deliver results to different on-premise and cloud systems, can support easy implementation of a complete KPI driven analytics pipeline. The modules allow manufacturers to implement workflows and level of complexity, at their own pace — supporting the theory of eating the elephant piece by piece. Besides directly supporting manufacturers, the low-code capabilities of Crosser’s solution have been relished by other industrial automation leaders.
In 2021, Crosser partnered with Paessler, a provider of automation software and network monitoring to provide customers with comprehensive monitoring of their IT and OT environments. Through pre-processing of OT data, Crosser supports Paessler’s Network Monitoring system to integrate
OT environments and devices into global monitoring. The need for digital transformation is imminent, but manufacturers must realize that there is no quick fix. Low-code offers manufacturers greater agility through real-time streaming and data transformation, which enriches data to create valuable insights that support organizational KPIs. Besides the direct impact low-code has on a facility’s performance, it also supports the workforce by lessening the reliance on external software developers and ultimately reducing the IT delivery gap.
Although low-code adoption on the rise, when implementing an IIoT strategy it’s important to remember to eat the elephant in pieces. Don’t try to swallow it whole.
About crosser technologies
Crosser is a Swedish software company with installations in over 20 different countries. We design and develop a Low-Code software platform for Streaming Analytics, Automation and Integration for any Edge, On-premise or Cloud. The Crosser Platform enables real-time processing of streaming, event-driven or batch data for Industrial IoT and Intelligent Workflows. It is the only platform of its kind that
is purpose-built for Industrial and Asset Rich organizations.
BY: Johan Jonzon, CMO and co-founder of edge analytics platform Crosser