Manufacturing in our post-Covid world
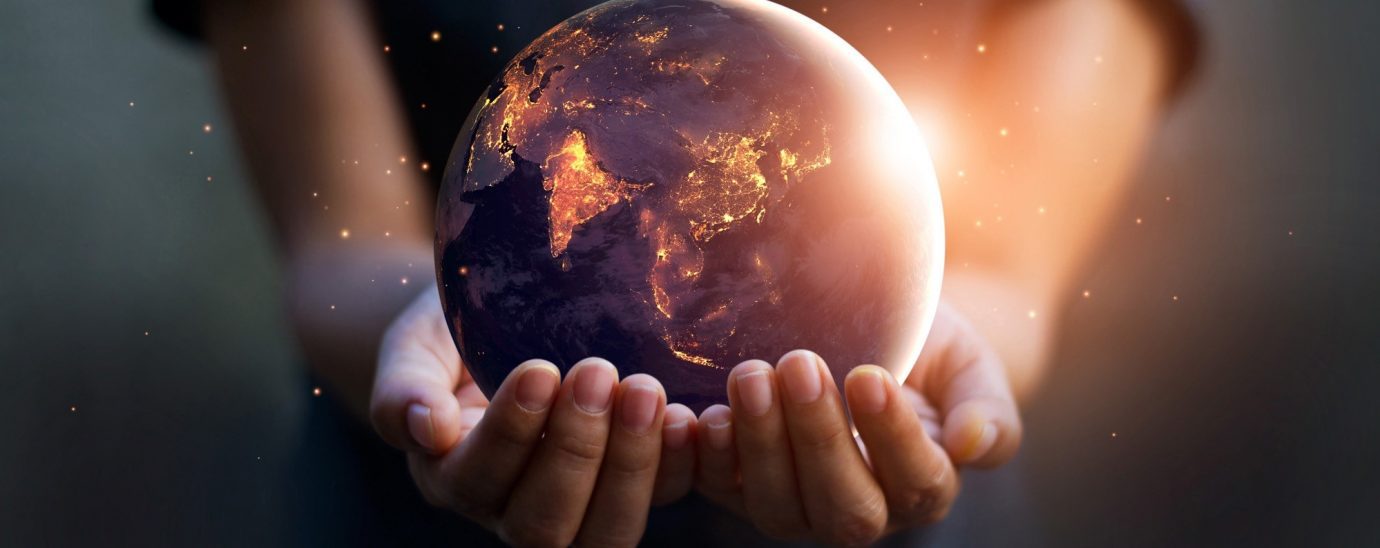
The historical importance of technological innovation in manufacturing is hard to overstate. The Industrial Revolution – which saw the transition from hand production to mechanization – laid the foundations for our modern way of life. Henry Ford’s assembly lines of the early 20th Century heralded a new age of mass production, travel and globalization. Yet until recently, many manufacturing companies have remained very traditional, slow to embrace new technology and make the move from mechanical to digital. Here Kimberly Kellermann, an engineer and Vice President of Global Operations for Global Industrial Packaging at Greif, explains why she thinks the pandemic could prove to be a turning point.
It was back in 1877 that the first Greif barrels were made in Cleveland, Ohio, and by 1908 the company was the largest cooperage plant in the world. Today, Greif is a global leader in industrial packaging products and services, still headquartered in Ohio, but with more than 16,000 colleagues in over 40 countries worldwide.
None of this growth and productivity would have been possible without innovation. One of the principles that guides our business at Greif is that we always look for ways to improve our work, products, services, and company, including continual improvement through new technology.
In terms of sustainability, for example, we have led the way as an organization in seeking innovative technological solutions to reduce our footprint and advance the circular economy. This has included developing a CMS to track and monitor our environmental compliance, supplemented by advanced EHS compliance and risk management software that identifies new and upcoming regulations applicable to each facility’s profile. Our CMS also collects and tracks waste, providing monthly access to data that helps to inform waste management efficiency. Digital innovation – in particular digitization and automation of manufacturing, digitization of supply chain and logistics, and digitization of purchasing and selling – is a particular driving force in our efforts to advance circular economy principles. As we continue to innovate, we analyze our entire value chain, from the extraction of raw materials through to our products’ end-of-life, to find opportunities to improve our products and processes.
However, as an industry as a whole, packaging manufacturing still relies heavily on manual and mechanized processes. While industries such as pharmaceuticals and aerospace were quick to respond to advanced manufacturing methods, ours has been slower to exploit the full potential of digital technology on the factory floor. In recent years, and even more now as a result of Covid, a significant labour shortage in manufacturing globally has prompted greater automation of simple processes and the reallocation of people to more skilled tasks. There is no doubt; however, many remain behind the curve when it comes to fully exploit digital advances such as cloud technology, AI, big data and the Internet of Things.
The Covid turning point
Pre-March 2020, visits, face-to-face meetings and extensive travel were part of everyday life for many colleagues at Greif. Equipment troubleshooting involved flying engineers and technicians around the world to diagnose and solve problems. When plants needed new equipment, a series of face-to-face meetings and visits were held to agree on requirements, determine specifications, carry out acceptance testing, check functionality and oversee installation.
This all changed abruptly as a result of Covid-19 restrictions. We began to share technical problems with our global experts virtually, allowing for quicker, more streamlined troubleshooting. On-site video streams were set up so we could carry out acceptance testing and checks and balances on equipment from home offices. We relied on the use of platforms like Zoom and Teams, with handheld cameras, mobile phones, video stabilizers and noise-cancelling headsets. Moving forward, we’re planning to pilot new virtual video capabilities and more immersive technology like Google glasses to provide real-time feedback.
This shift to virtual communications has inevitably had a major impact on the way we connect and learn on a day-to-day basis beyond the factory context. We’ve increased connectivity with our customer base through webinars and virtual plant tours, generating new business as a result. We’ve rolled out a global safety leadership programme via online workshops, video resources and training sessions. Our talent acquisition team has pivoted to virtual interviewing and onboarding.
Most memorably for me, in May of this year we had our first global virtual safety conference. We partnered with an audio-visual company to create a fully interactive, digital conference space that allowed people to access pre-recorded and live content, from talks and keynote speeches to safety games and quizzes. The event was a remarkable success, attended by delegates from 35 different countries. Feedback was overwhelmingly positive, with the enthusiastic response to activities reflected in the fact that our safety quiz was entered over 1000 times!
Assessing Impact
Working virtually has created significant cost savings in the short term, although it is too early to judge the long-term impact as we move towards a hybrid model. The introduction of new technology and processes has increased the speed and agility of many day-to-day tasks. Virtual meetings have enabled colleagues around the world to connect more regularly and to forge relationships on a broader basis. The reduction in travel has resulted in a reduction in emissions.
Perhaps more unexpectedly, innovation in technology has inspired innovation in other areas. Opening things up through virtual working has brought secondary benefits in terms of driving creative thinking and challenging the status quo. We’ve all been forced to take a fresh look at our ways of working and, in some cases, reprioritize to eliminate less value-added activity.
READ MORE:
- 5G could boost manufacturing by £6.3bn
- Achieving sustainability in a digitally connected world
- LPAs Key To Manufacturing Recovery
- Manufacturing at the Edge
Overall, I believe the acceleration in technological innovation that traditional manufacturing has seen since the pandemic will continue, albeit with virtual communication supplemented by more face-to-face meetings. The opportunity for tech companies to respond by developing new software and hardware to meet the needs of manufacturing organizations is immense. I look forward to seeing how technology innovation continues to transform our sector over the next decade.
For more news from Top Business Tech, don’t forget to subscribe to our daily bulletin!