Lightweight innovation for the aerospace industry
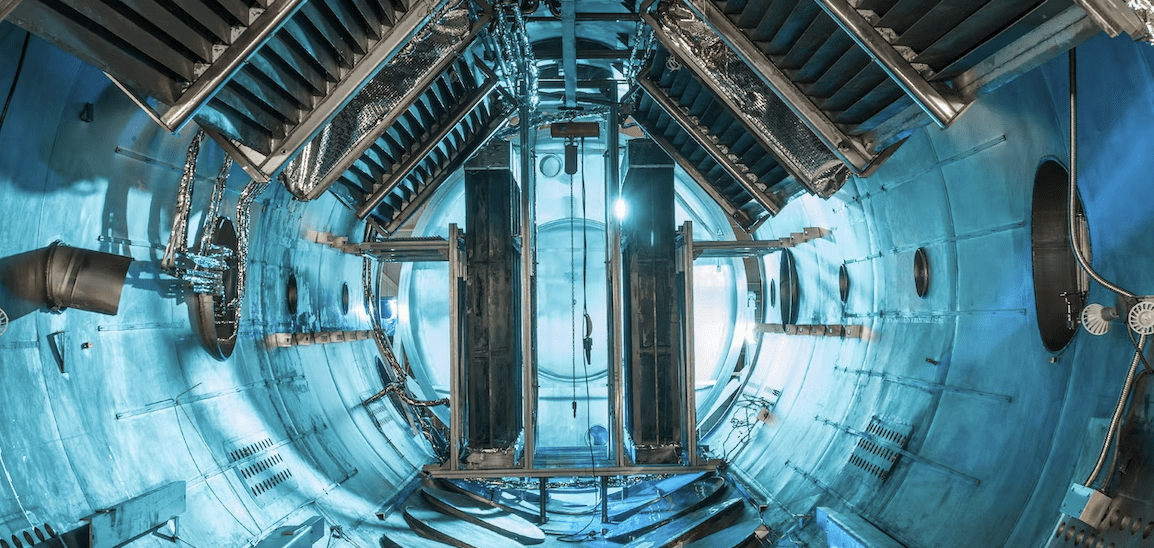
By transforming the way parts are designed and created, metal 3D printing provides an incredible game-changer for the aerospace industry with lightweighting opportunities. 3D Systems metal 3D printing rewrites the rulebook, as there is no longer any correlation between costs and complexity. The sky really is the limit.
3D Systems has been leading additive manufacturing (AM) innovation ever since the launch of the 3D printing industry in 1986. Dedicated to solving the biggest design and production challenges, they aim to push the boundaries by being the first in delivering and offering manufacturers the fastest solutions available to industries, including aerospace. 3D Systems gives their consumers the opportunity to unlock performance, and help their users defy conventional manufacturing limitations, accelerate and maximize the path to and value of AM.
Why lighter weight parts matter
Today, engineers have to deliver consistent improvements in parts and systems as a standard part of the job. In fact, lighter parts are the answer to driving up fuel efficiency, while cutting operating costs and emissions. However, swapping heavy for light is just the first step. The new innovative metal printing, also known as direct metal laser sintering (DMLS), direct metal printing (DMP), and metal additive manufacturing (AM), is what will give you the edge and set you apart from the competition.
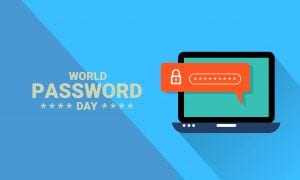
Metal 3D printing means a world of higher-order value propositions for engineers, where component consolidation increased performance, and supply chain efficiency is just some examples. When you look at the costs of keeping objects airborne or putting a rocket into space, lightweighting enters a league of its own.
Fuel Economy
In aerospace, even with modern advances in rocket re-use, sending a 22-ton payload into Low Earth Orbit (LEO) costs $62 million, or $2,818 per kilogram. This number can come closer to tens of thousands per kilogram for geostationary orbit. In civil aviation, every kilogram carried can cost an airline hundreds of dollars per year, per plane. When that weight and cost are multiplied across a fleet of aircraft, the total expense significantly increases.
On the other hand, just as costs add up quickly, so can savings. The lightweighting opportunities are overlooked and often forgotten, such as the non-flight-critical metal components in an aircraft cabin that can be hollow instead of solid. 3D Systems metal 3D printing offers hundreds of ways to take mass out and put fuel efficiency in.
For this reason, removing weight from a component or assembly using an additive manufacturing design, and production process can lead to impressive system benefits. By reducing the weight of components such as the reflectors of a communications satellite, your payload performance can drastically improve. As a result, the system improvements that stem from effectively deploying AM could enable new missions and make previously infeasible missions now possible.
Adding lightness with software
There are numerous software packages that can be used to design a lighter part. Most lightweighting workflows combine several of these packages, treating them as different tools in a toolbox. Some software is chosen simply to lay the groundwork design, while other packages offer advantageous simulation features. However, software that works seamlessly with CAD data is ideal and typically includes light-weighting tools such as lattice-builders. Similarly, some software can also optimize the additive workflow to fine-tune, prepare, and orient files as well as manage the printing process.
Add lightness with hardware and materials
3D files can be sent to print in a variety of metal alloys, including but not limited to aluminum, titanium, cobalt chrome, and stainless steel. When deciding which specific material or supplier to use, it is best to focus your efforts on those that have been thoroughly tested for the highest predictability of results. Given that less material is required for a lighter-weight part, material quality and performance are a worthy investment.
The advanced software, hardware, and materials enable users to benefit from investment casting workflows to cast 3D-printed molds in a fraction of the time and cost. Consequently, aerospace parts manufacturers can move directly from CAD to casting patterns with fewer design limitations and quickly create hollow patterns capable of greater design complexity without compromising functionality.
In Conclusion,
3D Systems provides more than just products – they offer a holistic portfolio of solutions with the experience and expertise to help you solve aerospace problems and deliver value efficiently and effectively. They focus on helping their customers use their additive technology to improve the driving experience and enhance productivity in many ways, such as reducing parts, lowering manufacturing variability, decreasing weight, and managing packaging constraints.
3D Systems knows that aerospace manufacturers rely on constant innovations to advance their industry. This requires the development of transformative applications capable of incorporating the latest engineering and design approaches, to optimize performance and gain a competitive advantage.
The Executive Vice President & Chief Technology Officer for additive manufacturing at 3D Systems, Dr. David Leigh says “I see the launch of this new platform – which includes a synchronous dual-laser option, Accura materials, and the specialized curing oven – as an example of how we are executing on a global AM strategy that focuses on our strengths.”
Today it is a competitive climate for lightweighting, and there are lucrative incentives on the other side of improvements. Considering the various advantages, applications, and potential of 3D printers in the aerospace industry, we can conclude that 3D Systems innovations will be seen in the next industrial revolution. Download the ebook here.