Unified data drives the factory of tomorrow
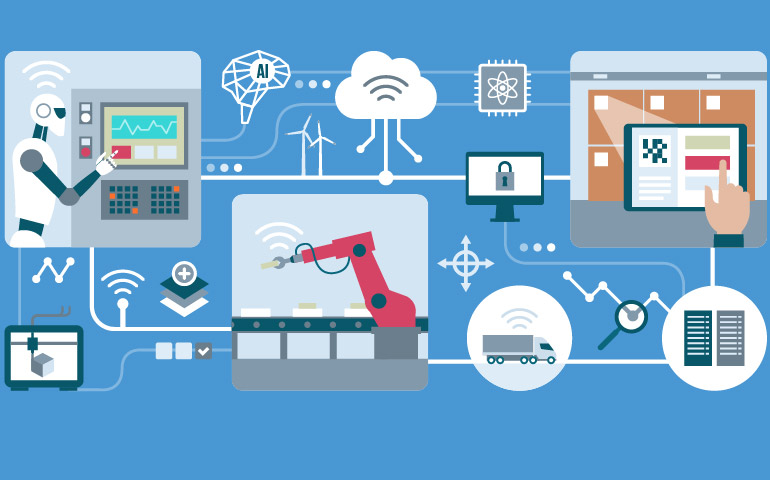
The factory floor presented a considerable array of workplace challenges through the first, second, and a good part of the third industrial revolutions. As we now drive through to the fourth industrial revolution with AI, the need for connected and integrated data-driven intelligence has never been higher, argues Alessandro Chimera, Director of Digitalisation Strategy at TIBCO.
Through the first (mechanisation), second (mass production) and a good part of the third (digital) industrial revolutions, the factory floor has presented a considerable array of workplace challenges.
Factory managers typically concerned themselves with safety, production efficiency, operational logistics and physical workspace innovation and development. Alongside where to locate the water-cooler, the tea and coffee facilities and how to create enough space for people to eat sandwiches at lunchtime, the factory of old ran a fairly standard template for the last century or more.
Things have obviously changed. As we now continue to drive engineering plants and the factory ‘fabrication’ sites that populate the 3.0 segment of the digital industrial revolution, we will now also start to think about the 4.0 era where industry also embraces a more data-centric approach to business.
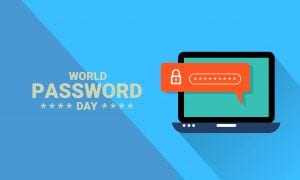
Manufacturing needs a 360-degree view of operations
To bring this new era of modern manufacturing online successfully, organisations will need to connect data across processes, equipment and Industrial Internet of Things (IIoT) devices intelligently. Tea and coffee will still be required, but businesses now need to think about how they will unify data for greater access and control. This data unification process is necessary because a manufacturing facility will naturally create different data sources over the years, but in their disparate and disconnected state, they can not provide insight into an end-to-end manufacturing process. Once data is unified and managed, the organisation can confidently predict the future to reduce costs, improve operations and increase profitability.
So, what are the mechanics at play here inside the modern digital-first factory? What should we think about in general terms, given that manufacturing has seen a traditionally slow uptake of digital platforms? Will all workers even need to get onto the factory floor as the next age of robotics is brought to bear, and, come to think of it, do we even need to wear overalls and steel toe-capped boots in the first place?
What we need to think about is how we are moving to a different way of working. Factory employees used to fill out operations sheets with information relating to work items carried out, defects detected, checks completed, etc. A typical factory in any industry might see hundreds of these production sheets daily, some of them being filled out electronically, but many of them still submitted on paper. Apart from the delay caused by data entry, even those work operations sheets entered electronically created a time lag.
This is not real-time, connected machine intelligence, but it should be, and it can be. Once our factories start to embrace the need for a unified view of end-to-end operational data, then we can start to engineer true efficiency gains for the future that will scale. At this point, we can not only vertically integrate machines with processes but also horizontally integrate the factory across all jobs, all work roles, and all workflows to ultimately create a unified view on end-to-end operational data.
Benefits of horizontal integration
The benefits of horizontal integration across the factory’s operational fabric break down into three core areas:
1) On the production floor: Always-connected machines and production units constantly communicate their performance status and, together, respond autonomously to dynamic production requirements. The ultimate goal is that smart production floors will cost-effectively produce smaller lot sizes and reduce costly downtimes with predictive maintenance.
2) Across multiple production facilities: If an enterprise has distributed production facilities, an Industry 4.0 approach promotes horizontal integration across plant-level Manufacturing Execution Systems (MES). In this scenario, production facility data (inventory levels, unexpected delays and so on) are shared seamlessly across the entire enterprise and, where possible, production tasks are shifted automatically among facilities to respond quickly and efficiently to production variables
3) Across the entire supply chain: Industry 4.0 proposes data transparency and high levels of automated collaboration across the upstream supply and logistics chain that provisions the production processes themselves as well as the downstream chain that brings the finished products to market. Third-party suppliers and service providers must be incorporated horizontally into the enterprise’s production and logistics control systems.
The speed of modern business
Modernised factories need to step up and run on a unified data backbone for many reasons, not least because the speed of business itself has changed.
Customers click away from online shopping carts without completing their transactions in a matter of seconds if a website’s functionality fails. But customers in the high street or shopping mall can jump upon a special offer in a shoe shop simply by walking inside; the online experience needs to be able to emulate that same speed of execution.
There’s also a digital-physical crossover. If a shopping mall offers customers the ability to scan a QR code or visit a URL to get an offer, then that price promotion needs to be executed in real-time, or customers will walk away. Likewise, the modern factory and its grasp of the supply chain, equipment management, goods production and dispatch has to run in the same fluid stream as the person who walks into the shoe shop.
A customer sees an offer; the customer looks; the customer confirms the purchase; the customer performs a transaction; the customer receives products within normally anticipated waiting time. This is the real-world shoe shop, and this is the real-time manufacturing business with the web front end.
Nullifying anomalies neutralises negativity
A key part of the progression to data-driven manufacturing is identifying, understanding and subsequently eradicating production plant anomalies created in real-time. This means we can avoid manufacturing waste by avoiding scenarios where we push the wrong or defective products (or perhaps services) through the production cycle.
In the case of manufacturing, an anomaly could be an occurrence of a machine breaking down, or it could be the supply chain having delivered raw materials that are damaged or not up to standard. An anomaly could be that a factory machine itself is misconfigured or simply not capable of providing a final product that falls in line with the company’s brand promise.
A manufacturing operation can grasp its need for anomaly management and build the information relating to anomalies into its unified approach to data through the use of Real-Time Performance Indicators. These could be sensors, or they could be practices related to quality measurement, gauge customer satisfaction, or some more straightforward measure of inventory.
As an illustrative working example, a power switch manufacturer in central Italy used data to gain an operational advantage after discovering a machine performance anomaly. When the blades in one of its production machines failed to fit or engage, its IT team built a data model to analyse many factors from the factory floor.
The factory found that its blades did fit if the indoor temperature was 2 degrees Celsius lower than the average temperature recorded. The business could also use digital twins with enough properties and attributes to describe the shape, size, temperature, airflow etc., inside the factory floor area. But the company was only able to get the insight needed by ensuring that it had good quality data and the ability to get a connected end-to-end view of all data streams available.
The road ahead, with remote operations
The road ahead is one with digitally-empowered manufacturing facilities where data-driven insight maximises Overall Equipment Efficiency (OEE). This makes for a more productive, more profitable and more highly performant factory and a facility with reduced scrap and waste levels, reduced energy requirements, and lower downtime. These factors combine to create a more efficient plant with much-improved product traceability from front to back and end to end.
To embrace the concepts and approach on offer here and move towards a more remote factory operations setup, we need to ensure that we have a consistent and unified view of good quality data. Estimates suggest that we could reduce the number of on-plant workers by as much as 75% and repurpose these employees in higher-value, often more personally fulfilling roles.
Demonstrating such a forward-thinking approach is Hemlock Semiconductor, the largest polysilicon producer in the United States, which provides this vital material to companies worldwide. It then uses it to produce the silicon substrates used in high-tech electronics solar panels.
To solve the joint challenges of cost, quality, and conservation, Hemlock needed an operational strategy that would strengthen its long-term profitability and competitive positioning and embark on a multi-step journey to transform every aspect of its manufacturing process digitally.
By connecting all systems, unified data flows, and optimised analytics for a real-time 360-degree views of all facility and manufacturing operations, not only was it able to control costs and quality better with a data-centric approach, but now has complete visibility into processes. New opportunities are illuminated, and potential new business models the company could take advantage of. Hemlock was able to take advantage of new market segmentation because it had built a data-centric view of its manufacturing processes, allowing it to further optimise yield by selling the right product to the right market at the right price.
Working smarter, better, faster
Where we still have an engineer on the factory floor with a spanner and screwdriver in hand, they will be able to work smarter, better and faster. Where they once wandered between machines looking for possible faults and tinkering with dials to look for fragilities, data will now direct these workers to the right machine and the right screw or bolt, all at the right time.
READ MORE:
- The future of work: driving employee engagement in a hybrid working landscape
- How Wi-Fi6 will optimise hybrid working
- Which European countries have the best and worst cybersecurity?
- McAfee: How to make telehealth safer for a more convenient life online
The factory overall and boots making business won’t be going out of business tomorrow, and we will still need water-coolers, tea, coffee and sandwiches, but even these factors will be digitally tracked so that staff canteens have all the right items for enough people at the right time. The future of work is smarter and just that little bit less filled with industrial grease under the fingernails. But please, keep washing your hands.
For more news from Top Business Tech, don’t forget to subscribe to our daily bulletin!