Fixed vs Flexible Intralogistics Automation & Why Companies Often Need Both
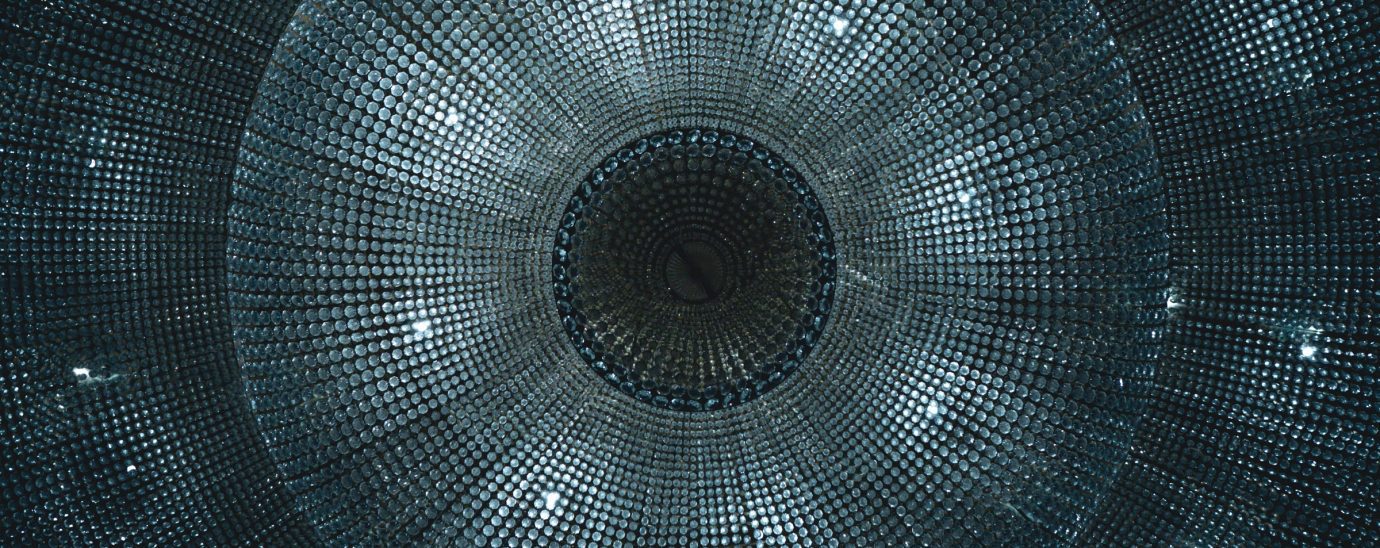
Often Need Both With supply chain disruptions not entirely mitigated and with a shortage of labor, the demand for reliable warehouse automation is higher than ever. Different challenges require different types of automation, both fixed and flexible, but many automation companies only offer one style of robotic automation which may not be enough.
Pieter Feenstra is the CEO of Addverb Technologies’ EMEA region. Addverb’s expertise includes IoT, robotics, and warehousing consulting. Addverb has provided warehouse automation solutions to companies such as Unilever, Amazon, Flipkart, PepsiCo, Coca-Cola, ITC, and more. Consumers around the globe have experienced the effects of production slow-down in recent months.
Although many industries are seeing the light at the end of the post-COVID tunnel, the high demand for retail and fast-moving consumer goods (FMCG) products has caused a new wave of complications in the labor market. Many companies in FMCG, retail, and e-commerce have been forced to reckon with the growing demand for both in-store and online products. Simultaneously, the labor market has reached a status of almost zero unemployment proving it very difficult to keep up with the demand.
A 2020 study by the Workforce Institute, a workforce, and human resources management company, found that even before the COVID-19 pandemic, there were projections of a 6 million-worker shortage in manufacturing by 2030. On top of that, the move to reshoring due to the pandemic adds another element to the labor shortage issues.
That same study found that 62% of hiring managers had difficulty recruiting skilled talent and 44% of hiring managers experienced higher-than-average voluntary turnover in the year leading up to COVID-19. If there are not enough workers to do the required order-picking and handling in warehouses, a dilemma presents itself: Companies must decide whether they’d like to further automate their logistics processes or perhaps will face the problem of no longer being able to deliver the products on time.
Automating logistics with robotics not only means lowering costs – it also means keeping up with today’s high demand. Finding the right hardware automation for different types of orders is a challenge, especially if both types of orders are handled from one logistics center.
For example, automation requirements are often very different for store deliveries (which tend to be more stable and predictable) than for online orders. There are a couple of different options that companies can choose to suit their specific needs best.
The first is fixed automation. Fixed automation has been a tried and tested option for decades and is used mostly for deliveries from FMCG to retail or from retail to store. With fixed automation one should consider solutions with stacker cranes or shuttle systems (think fixed racking, rails, etc) and it requires roller conveyors around it to bring pallets or boxes to and from a warehouse.
One of the highlights that fixed automation yields is that it can handle high storage density that can use the full height of buildings. Fixed automation robots are carefully calculated for a predictable flow and can then give a very good return. For a long-term stable flow, fixed automation is one of the best solutions.
Where fixed automation’s atrophy shows are in less-predictable scenarios. E-commerce, for example, can have high peaks and massive changes from year-to-year or even season to season. Fixed automation would not be able to necessarily keep up with the changing times. E-commerce companies might benefit from more of a flexible automation approach.
As the name suggests, flexible automation allows manufacturers or logistics companies to quickly alter production capacities or warehouse capacities as needed. Where adaptability and scalability are required, this kind of automation tends to be the number one choice. Many e-commerce companies need automation due to their demand but do not yet know what their future demand will look like. Flexible automation allows these companies to start with a certain set of robots and then scale up or down or combine with other robots when required.
This is where the rise of certain companies such as Geek+, Hai Robotics, Exotec, and our company Addverb have come into play. Oftentimes, flexible automation solutions also need a shorter time to implement as it makes use of standard robots. This grants companies the option to lease, rent, or go for robots as a service (RaaS).
More often than not, companies have a part of their business relatively stable and predictable, although some aspects of their business remain uncertain. For example, retail chains often supply stores but sell more through their e-commerce business. This especially grew exponentially during COVID and now remains a large aspect of many businesses. This is why a combination of fixed and flexible automation must be at the ready for companies’ distribution logistics. The intralogistics and warehouse distribution industry are growing every day and this comes with new challenges.
Automation robots as hardware powered by software can ensure a smooth end-to-end supply chain distribution process. At the same time, the question should not be whether companies should choose fixed or flexible automation, but how to determine the right combination of fixed and flexible for their specific needs. With these blends, there is an optimum of automation addressing the labor scarcity for the different channels to markets of the customers.
Companies and manufacturers that find themselves stuck in the fixed vs flexible automation systems dilemma might benefit from asking themselves the following questions concerning expectations of their warehouse operations:
- What part of my business can I reasonably predict for the coming years?
- What part of my business can I reasonably predict for the coming years?
- Can I still fulfill the requirements of my customers?
- How long can my current buildings support my warehouse operations with my current way of working and are there different solutions that can extend this period?
- Do I have the most cost-efficient solution to run my warehouse? The answers to those questions may point companies to the right solutions for specific challenges.